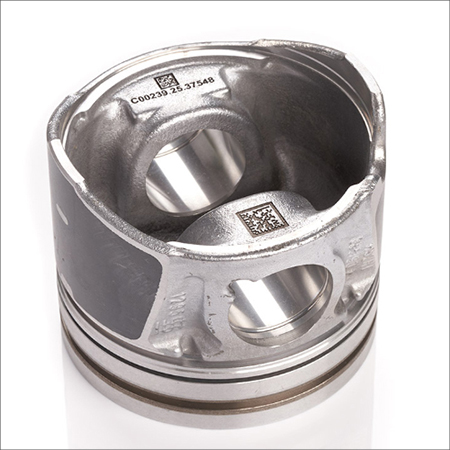
Materials & processes
Applications
With the innovative laser processing machines from ACI Laser, you can mark various materials – such as metals, plastics, ceramics and foils – permanently and with high quality. The laser systems work with high precision and offer flexibility, speed and environmental friendliness.
The laser solutions are suitable for many industries, such as the automotive industry, supplier industry, medical technology, mechanical engineering and many more.
Laser marking is a high-quality, efficient and fast method for robust and permanent markings. It is superior to other methods.
Laser engraving is a robust and scratch-resistant marking method for many materials. It can withstand temperature, liquids and coatings.
Laser trimming is a method of adjusting resistors with a laser. There are two types: passive trimming for special values and active trimming for circuit optimization.
Black marking creates a high visual contrast without damaging the surface mechanically.